Warehouse racking options are diverse and tailored to accommodate various storage needs, inventory types, and operational requirements. As an expert in warehouse management, I'll outline several common racking options along with their key features and suitability for different applications:
Selective Pallet Racking
Selective pallet racking is a versatile and widely used storage solution that provides direct access to every pallet stored. It consists of upright frames and horizontal load beams, allowing for easy adjustment to accommodate different pallet sizes and configurations. Selective racking is ideal for warehouses with high product turnover and a wide range of SKUs requiring frequent access.
Drive-In and Drive-Through Racking
Drive-in and drive-through racking systems maximise storage density by eliminating aisles between racks. In drive-in racking, pallets are loaded and retrieved from the same aisle, whereas drive-through racking allows access from both sides. These systems are suitable for storing large quantities of homogeneous products with low turnover rates, such as seasonal items or bulk goods.
Push Back Racking
Push back racking systems utilise nested carts and inclined rails to store pallets in a Last-In, First-Out (LIFO) configuration. This system offers higher storage density compared to selective racking while still providing relatively easy access to stored items. Push back racking is suitable for warehouses with moderate SKU diversity and varying inventory turnover rates.
Cantilever Racking
Cantilever racking is designed for storing long, bulky, or irregularly shaped items such as lumber, piping, or furniture. It features horizontal arms that extend from upright columns, providing unobstructed access to stored items. Cantilever racking is adjustable to accommodate varying item sizes and lengths, making it ideal for warehouses with oversized or non-standard inventory.
Pallet Flow Racking
Pallet flow racking, also known as gravity flow racking, utilises inclined roller or wheel tracks to facilitate First-In, First-Out (FIFO) pallet rotation. Pallets are loaded into the rear of the system and move forward under gravity as pallets are retrieved from the front. Pallet flow racking is suitable for high-volume, high-throughput operations with perishable or time-sensitive inventory.
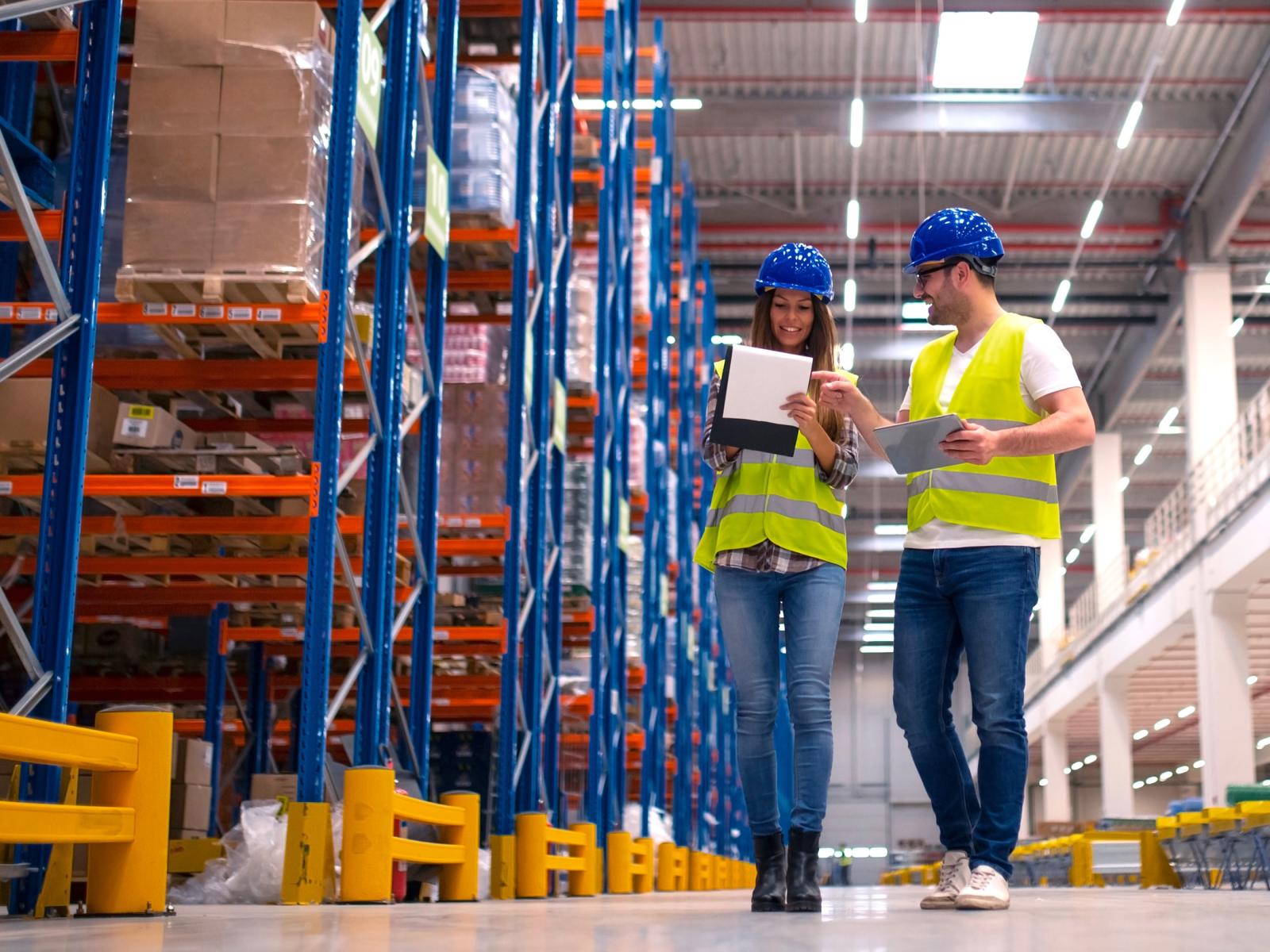
Shuttle Racking
Shuttle racking systems employ automated shuttle vehicles to transport pallets within the racking system. This allows for dense storage and high throughput, as pallets can be stored and retrieved from deep within the rack without the need for manual handling. Shuttle racking is ideal for warehouses with a large volume of homogeneous products and high turnover rates.
Vertical Lift Modules (VLMs)
Vertical lift modules are automated storage systems that utilise vertical carousels to retrieve and store items stored in trays or bins. VLMs maximise storage density by utilising the full height of the warehouse while providing high-speed retrieval and accurate inventory management. VLMs are suitable for warehouses with limited floor space and high-value or small parts inventory.
Each of these warehouse racking options offers unique advantages and considerations. By evaluating factors such as inventory characteristics, space constraints, and operational workflows, warehouse managers can select the most suitable racking solution to optimise storage efficiency, accessibility, and overall warehouse performance.